Urethane Casting
Casting offers a low cost way to produce low volume production and prototyping from 10 to 100 parts. Ask our engineers about all the cast in colour and finishes available.
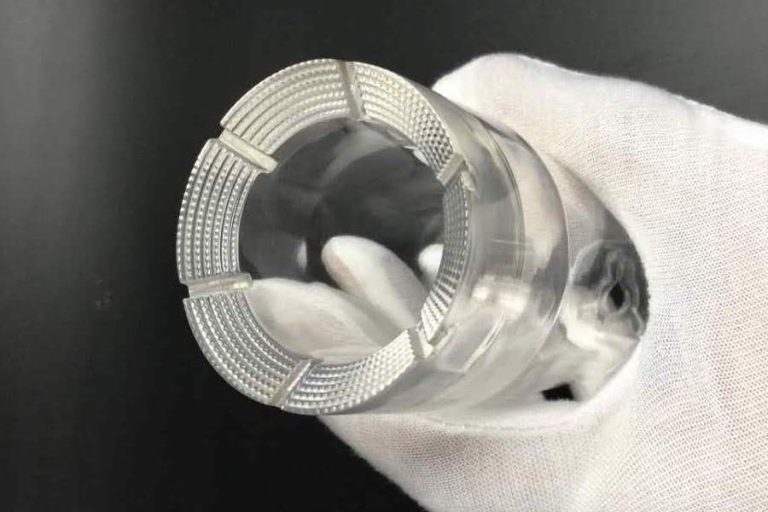
Certifications
IATF 16949: 2016
ISO 9001: 2015
30+ Materials
Choose from both rigid and flexible PU materials
> 36" Large parts
Economical way to produce low volume large parts
Over-mold Parts
Ability to produce over-molded dual hardness parts in low quanitiies
Urethane Casting Services
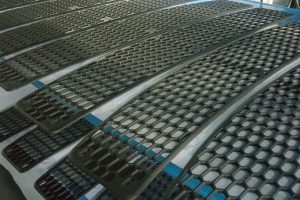
Low volume production
Production parts as fast as 7 days with low minimum order quantities.
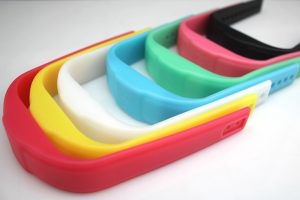
Cast in colors and finishes
Just like injection moulding we have the ability to formulate
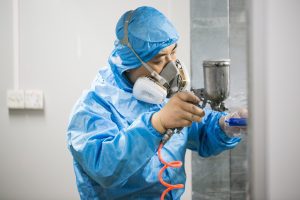
Surface Finishing
Add multiple finishes to your part such as anodizing or powder coating.
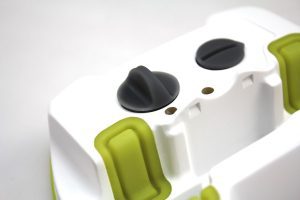
Over molding
Production quality parts without the tooling investment.
Urethane Casting Service Advantages
Production Quality at Low Volumes
This process is a quick, cost-effective way to produce 10-200 units with production-level quality. Typically, each silicone mold will produce 20 castings.
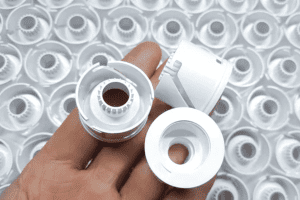
Complex Elastomeric Parts
Urethane casting is ideal for prototyping elastomeric parts such as complex gaskets and overmolds on rigid parts.
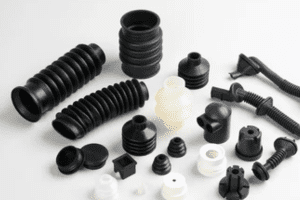
Engineering materials
Urethane casting allows for almost limitless complexity, including sharp internal corners unachievable with CNC machining, and designs without draft or uniform wall-thickness that can’t be injection molded.
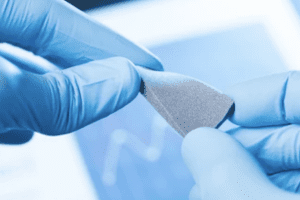
Why choose RP Group for Urethane Casting?

Design for Manufacturing
Our experienced engineer will analyse your design and provide you with a Design for Manufacture (DFM) report to discuss manufacturability and also look for opportunities to reduce cost.

Communication
We are always quick to respond to questions via email, phone, web meeting or chat to ensure your project is turned around as fast as possible. All project history kept on our secure online portal.

Quality Reports
All projects where 2D drawings are provided come with a dimension report before parts are shipped. We can provide CMM reports on demand at no additional charge.

Transparent Progress Reports
Using our customer portal, we provide real-time progress and tracking information. Videos and photos of the parts can be confirmed before parts are shipped out.

Manufacturing Speed
At RP Group we have in-house rapid prototyping as well as mass production capabilities which has helped our customers accelerate their products to market.

Full Service Manufacturing
We offer a wide range of materials, processes, finishes and sub-components to make us your one-stop supplier for your entire project.
Surface finishing
In our in house painting, printing polishing shop and we can offer a wide range of surface finishes such as EMI shielding paint, printed logos, automotive grade 2K paint, rubber/soft touch paint and UV clear top coat and many more ...
- In house paint shop
- Screen and pad printing
- 2nd operations and assembly
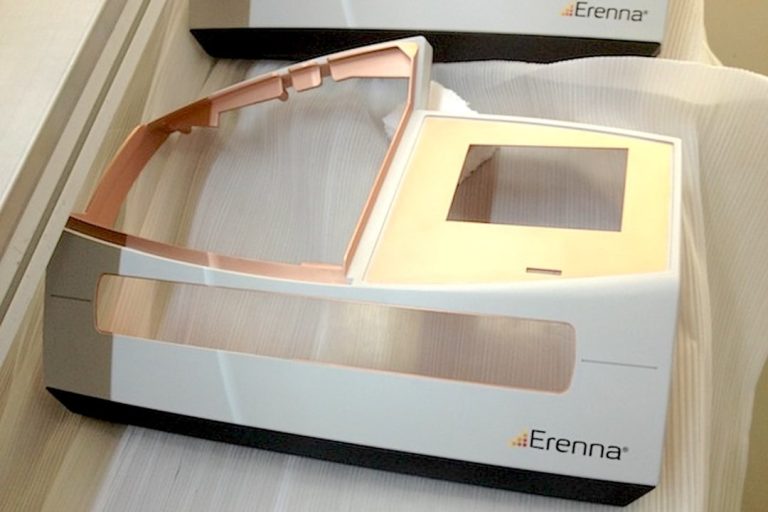
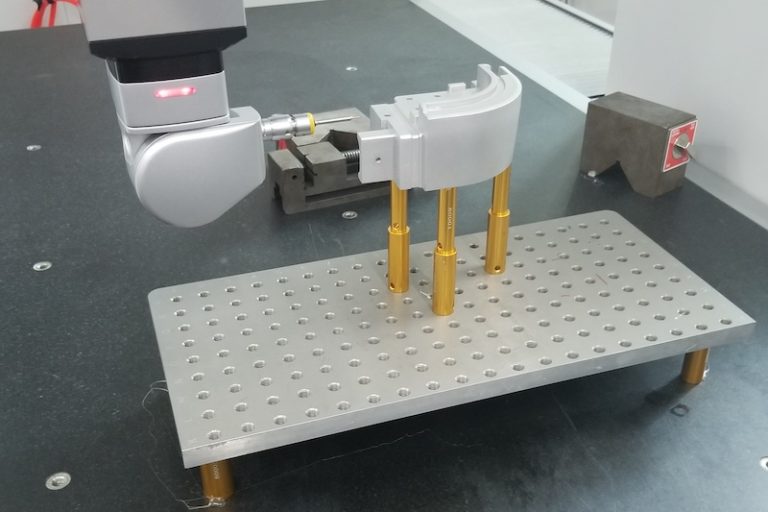
Metrology
At all four of our RP Group manufacturing locations, we have a fully equipped metrology department to ensure your part's quality compliance. Experienced engineers in fixture and gauge design from GD&T.
- Programable Hexagon CMM machines
- Full range of calibrated metrology equipment
- Check fixtures and gauges from GD&T
Urethane Casting FAQs
Have a question that not listed below? Please contact us today to get more information.
Urethane casting is a 3 step process:
1) Create a master. This part will used to create the silicone mold and it can either be 3D printed or CNC machined. The final surface finish is added to the master so it will appear on the mold.
2) Create the silicone mold. Gates, part lines and air vents are added to the master and then liquid silicone is poured over the master to make the mold. After the silicone has set or hardened the mold is cut open and the master is removed.
3) Parts are casted under vaccuum. When the different parts of the PU material is mixed a gas is given off. We use specialized casting machines that mixes and pours the PU material automatically under a vaccuum to avoid bubbles in the parts.
4) Gates, flash, and venting removed: The gate, flash (extra material that comes out between the 2 halves of the mold), and the vents are cut off the parts and polished smooth if required.
5) Final surface finish applied: The parts can be polished, painted or printed according to customer requirements as well as assembled with components such as brass inserts.
This depends on the part complexity, surface finish and the silicone mold material. With the most economical grade of silicone the mold life is approximately 12 shots/parts and for the higher grade (4 x as expensive) the mold life is approximately 25 shots/parts. For very complex parts with many under cuts the mold may break up before 12 shots/parts although the same master can be used create another mold for higher volume production.
1) Fast product development: Gives you the ability to test the market quickly and without a large investment in hard steel tooling and therefore avoid the large delays to get to market and the high costs of engineering changes. After the market and the design is validated or confirmed you can then move on to high volume steel injection molds.
2) High quality low volume production: It can provide high quality low volume production for products such specialized machines like bench top medical laboratory equipment.
3) Design freedom: You can create complex and detailed geometries so it can offer a lot of freedom that other processes cannot provide.
4) Time to market: You can accelerate the time to market by either creating high quality final production parts or use the higher quantity prototypes to test out production assembly lines and provide more production representative sales samples for your business development team.
5) Material selection: A wide range of finishes and material types from flexible to to rigid glass reinforced materials are available.
6) Part finishes: Various production textures, surface treatments and custom colors are available so you don't have to compromise on the final look of your product.
1) Upfront investment in molds: This is much higher for injection molding although due to the mold life when amortized over high volumes of part production there is a break even point where injection molding becomes cheaper. We can help make this analysis for your decision making of cost verses time verses quality.
2) Material costs: Costs of production materials are in general cheaper for injection molding although there is the added high cost of minimum order quantities and waste due to machine set up that make urethane casting a lot cheaper in this situation.
3) Lead time: For mass production steel injection molds the lead time can take months as they need to be carefully designed and machining of the hardened steel take a long time and then further delays to tune and make any necessary engineering changes and post treatment. Urethane molds can be made in days and cast urethane parts from the silicone molds can be shipped within a we