Sinker EDM Service
Sinker EDM can be used to create hard-to-reach, angular internal features such as blind keyholes which cannot be machined using other methods.
Contact us for more information.
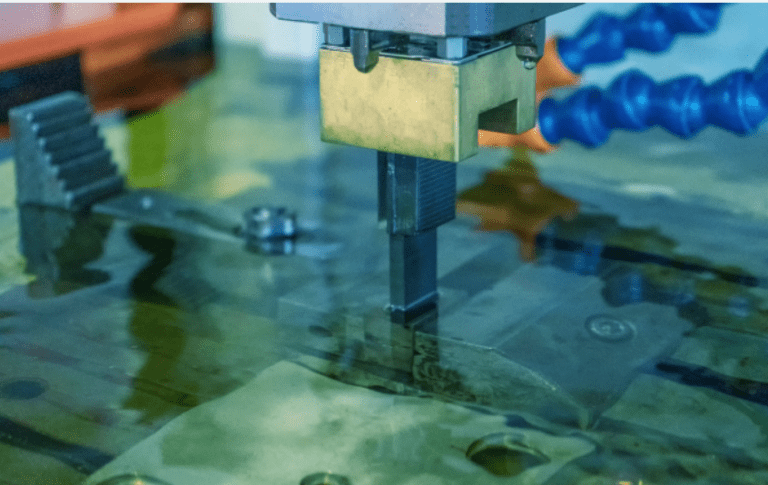
Certifications
ISO 9001: 2015
IATF 16949:2016
40,000+
Machined parts each month
50+
CNC machines
100+
Plastic and metal materials
What is Sinker EDM?
The Basics of Sinker EDM
Sinker EDM is a subtractive manufacturing technique that uses spark erosion to produce extremely precise parts. Flash disintegration alludes to the cycle where a device, called a terminal, makes holes in metal workpieces. The fact that the electrode sinks into the raw material gives sinker EDM its name.
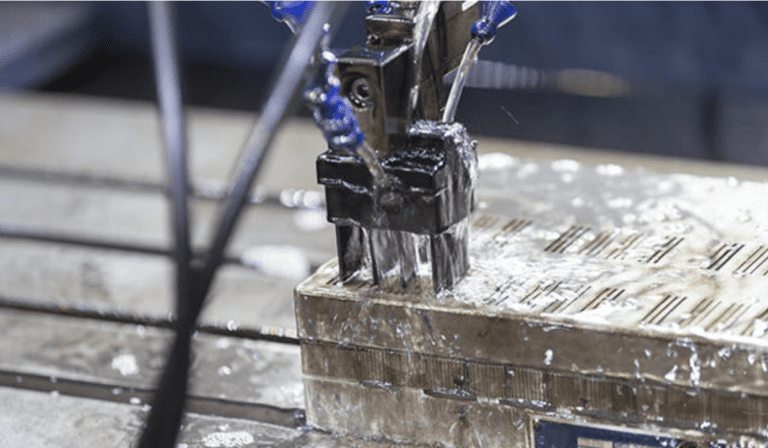
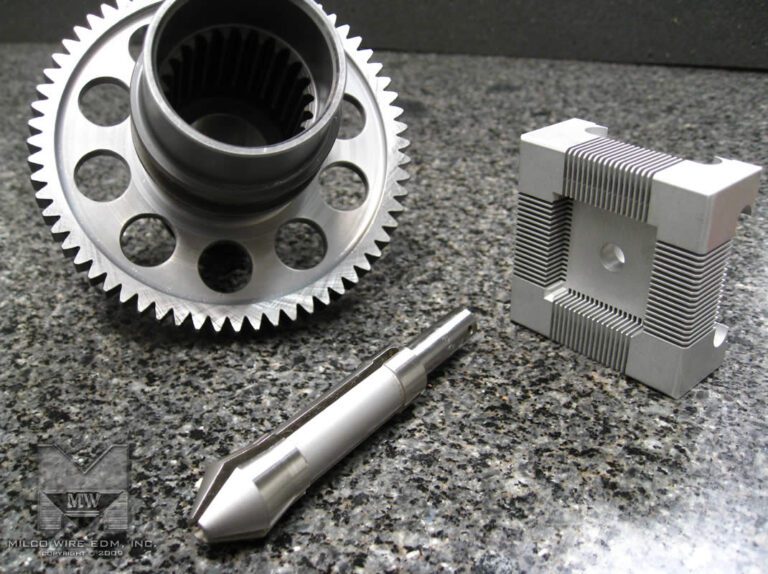
How Sinker EDM Works
Sinker can make complex geometries that Wire EDM can't. Typically, the electrode material is copper or graphite that has been machined into a particular shape that is the opposite of the part's intended final geometry. After the electrode has been shaped, a process known as "electrode wear" causes the workpiece to be damaged by sparks that form the right shape. Sinker EDM, in contrast to Wire EDM, is capable of making both partial and complete cuts through the workpiece.
All CNC Machining Services
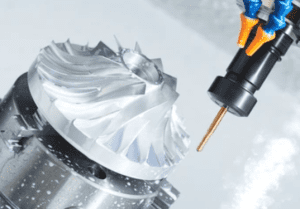
CNC Milling
3, 4 and 5-axis machining of plastic and metal parts. Machine up to 66" in size*
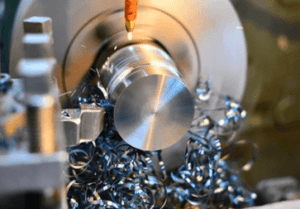
CNC Turning
Tight tolerances and finishing capabilities, as fast as 2 days.
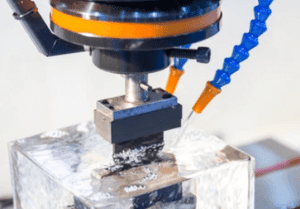
Sinker EDM
Create blind holes and complex cavities using sinker EDM machining.
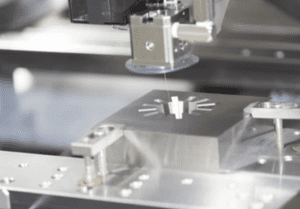
Wire EDM
Cut a 2-dimensional profile out of very thick material using wire EDM
CNC Service Applications
Low Volume Production
RP Group offers full production-quality parts in volumes ranging from a single piece to a few thousand pieces.
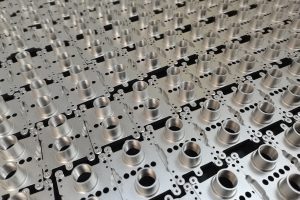
Appearance Prototypes
We take pride in producing the finest appearance models and prototypes with very high detail in any material you want.
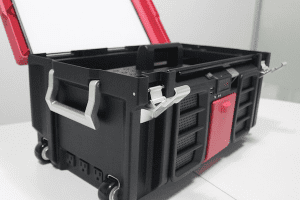
Fixtures and Gauges
We engineer fixtures and gauges to your specifications and may offer recommendations based on our in depth understanding of Geometric Dimension and Tolerancing (GD&T).
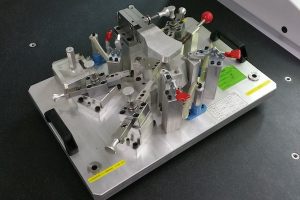
CNC Machining Materials
Metals
- Aluminum
- Brass
- Copper
- Stainless Steel
- Steel Alloy
- Magnesium
- Titanium
Plastics
- ABS
- Acetal
- CPVC
- HDPE
- LDPE
- Nylon
- PEEK
- PEI
- PET
- PMMA
- Polycarbonate
- Polypropylene
- PPSU
- PS
- PSU
- PTFE
- PVC
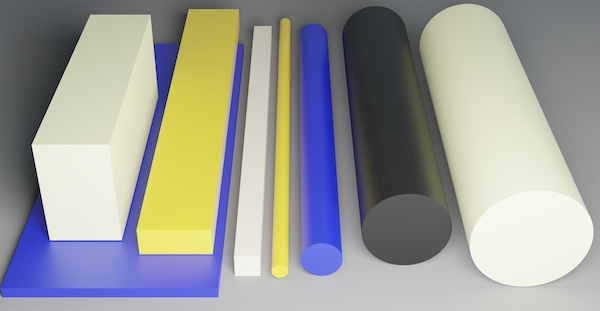
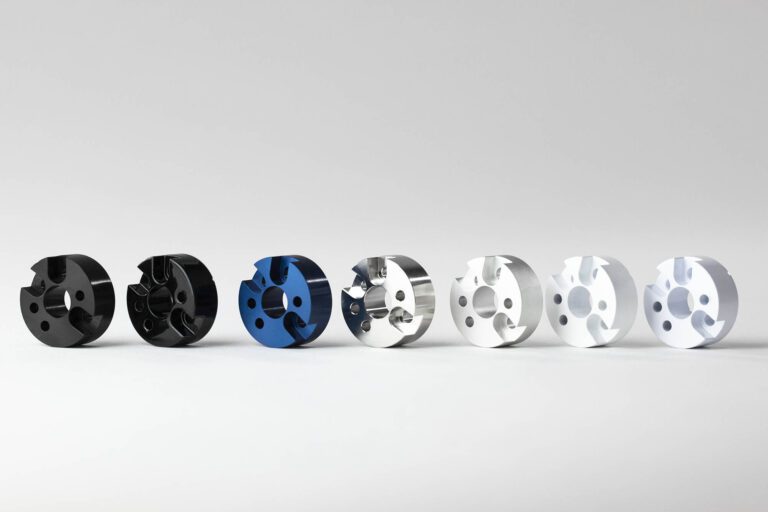
Finishing Options
At RP Group we can generate instant quotes for 10+ surface finishes. We can help you select the right finishes for your applications.
CNC Precision Machining Tolerances
At RP Group, we use ISO 2768 standards for CNC machining.
The length of parts that RP Group accepts depends on the machining process, with some processes accepting parts up to 48 inches in length. For larger parts, it is recommended to get in touch with RP Group's team.
It should be noted that the tolerances indicated are minimums in an optimal scenario and looser tolerances may be necessary based on the process, material selection, or part geometry.
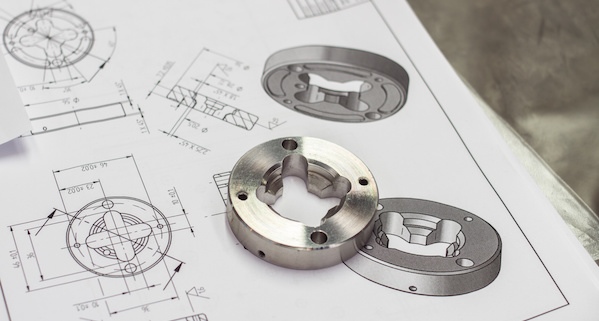
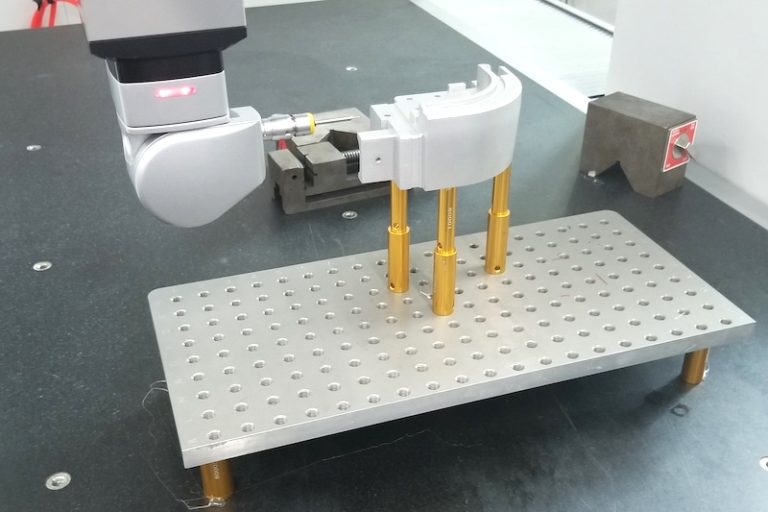
Metrology
At all four of our RP Group manufacturing locations, we have a fully equipped metrology department to ensure your part's quality compliance. Experienced engineers in fixture and gauge design from GD&T.
- Programmable
- 3D Scanning
- Fixture and gauge manufacture
Design for Manufacture (DFM) is important part of product development to save money and improve quality
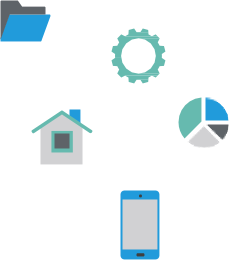
Why choose RP Group for CNC Machining?

Design for Manufacture
Our experienced engineers will analyse your design and provide feedback on manufacturability and look for opportunities to reduce cost.

Communication
We are always quick to respond to questions via email, phone, web meeting or chat to ensure your project turn around is as fast as possible.

Quality Reports
All projects where 2D drawings are provided come with a dimension report before parts are shipped. CMM reports can be produced on demand at no additional charge.

Transparent Progress Reports
We provide progress and tracking information through our customer portal. Videos and photos of the parts can be confirmed before parts are shipped out.

Time to Market
We have a infinite capacity via our vetted supply chain outside our own in house capabilities so we have the flexibility to manage all projects large and small.

Full Service Manufacturing
We can offer a wide range of materials, processes, finishes and sub-components to make us your one-stop supplier for your whole project.
Sinker EDM FAQs
Although wire EDM accuracies of +/- 0.00004" (0.001mm) are occasionally mentioned, it is more commonly accepted that a tolerance of +/- 0.0002" (0.005mm) is achievable. It is important to note that the accuracy of EDM is influenced by factors such as the properties of the workpiece, the desired surface finish, and the available machining time.
An EDM surface finish is distinct from one made by conventional methods of material removal. The texture is random rather than showing directionality, which is advantageous for numerous applications. Additionally, multiple skimming passes can achieve almost mirror-like finish quality with EDM.
Sinker EDM can be used to machine a wide variety of conductive materials, including hardened steel, titanium, tungsten carbide, and even diamond.
Sinker EDM is a slow process compared to other machining methods, and it can be difficult to machine deep or narrow features. It also requires specialized equipment and skilled operators.
Several factors can affect the performance of sinker EDM, including the type of material being machined, the size and shape of the electrode, the dielectric fluid used, and the electrical parameters such as voltage, current, and pulse duration.
While both sinker EDM and wire EDM use electrical discharge to machine materials, they differ in their electrode configurations. Sinker EDM uses a shaped electrode to create a specific shape in the material, while wire EDM uses a thin wire to cut through the material.