Understanding the Basics
Before delving into the differences, let’s establish a foundational understanding of CNC machining:
3-Axis CNC Machining:
- Utilizes three axes – X, Y, and Z – to move the cutting tool along three directions.
- Suitable for machining relatively simple parts with flat or prismatic geometries.
- Commonly used in industries where precision is crucial but complex contours are not a primary requirement.
4-Axis CNC Machining:
- Incorporates the three standard axes (X, Y, and Z) and adds a rotational axis (typically A or B).
- Enables the cutting tool to move along an additional axis, offering more flexibility for machining complex geometries.
- Ideal for parts that require features such as undercuts or holes at different angles.
5-Axis CNC Machining:
- Includes all the features of 4-axis machining with an additional rotary axis (C).
- Enables the cutting tool to tilt at various angles, allowing for machining complex contours and shapes.
- Widely used in aerospace, automotive, and medical industries for producing intricate parts with high precision
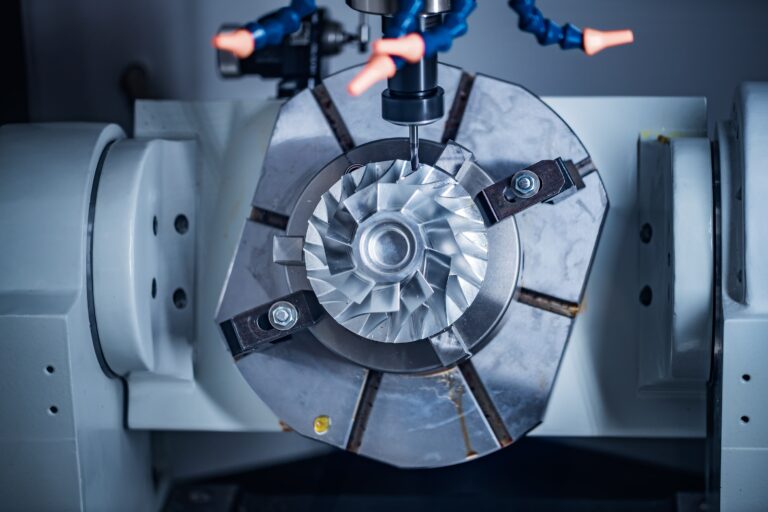
Diving Deeper into Distinctions
1. Complexity of Parts:
- 3-axis machines are best suited for simpler parts with straightforward geometries.
- 4-axis machines provide the capability to machine more complex parts by adding rotational movement.
- 5-axis machines offer the highest degree of complexity, enabling the machining of intricate and contoured surfaces with fewer setups.
2. Setup Time and Efficiency:
- As the axis count increases, so does the setup complexity and time required.
- 3-axis machining is generally quicker to set up compared to 4 and 5-axis machining.
- 5-axis machining, while more time-consuming to set up, often results in increased efficiency and reduced production time for complex parts.
3. Tool Access and Surface Finish:
- Higher-axis machines provide better tool access to complex surfaces, reducing the need for multiple setups.
- 5-axis machines, in particular, can achieve superior surface finishes due to their ability to approach the workpiece from multiple angles.
Conclusion
In CNC machining, selecting between 3, 4, and 5-axis capabilities depends on part complexity and efficiency goals. As technology advances, these techniques will play a key role in shaping precision manufacturing’s future, opening up possibilities for intricate components. Whether working on simple or complex designs, understanding these machining methods is crucial for achieving the best results in precision engineering’s dynamic landscape.